超厚5G天线模块制作工艺研究
超厚板二钻精度控制
客户对定位精度有特殊要求,孔中心位置偏差要求按±0.05mm控制。因此需要预钻小孔,使内层盲孔制作时先预钻小孔,以减少总压钻通孔的阻力,降低断刀风险。同时采用板边菲林孔定位测量涨缩,为钻孔文件提供精确的尺寸涨缩信息。最后在钻孔加工过程中,要使用刃长12mm直径1.65mm新钻刀,一步下钻方式,一次钻透NPTH安装孔,防止分步钻孔造成精度偏差,效果如下图4所示。
图4 二钻后隔离环无明显偏移
超厚板外形加工及热冲击效果
由于成品板过厚,需要采用正反控深铣的方式加工,外形设计顶层、底层两组文件,从正、反两面各控深6mm做外形加工。此外定位方式以板内1.65mm-NPTH孔做内定位,防止外形偏移。完成加工后检测外形,设计尺寸为32.5mm*32.5mm*11.4mm,实际检验尺寸偏差≤0.10mm,板边光滑平整,符合品质要求,如下图5、图6所示。
图5 外形后边缘质量 图6 外形尺寸测量
对成品进行耐热性测试,在热冲击条件288℃/10S/3次条件下,未出现分层爆板现象。
图7 热冲击无爆板分层(热冲击条件288℃/10S/3次)
总结
本文提供了一种11.5mm超厚板的生产加工方法,并通过工艺改进,有效解决了业界常见的技术难题:
1、超厚板层压技术:常规水平线加工板厚上限在7.0mm左右,本次通过结构优化,将通孔+背钻优化为两次盲孔分压,有效满足了超厚板的层压、电镀及蚀刻要求。
2、超厚板表面处理工艺:通过流程优化,将阻焊及表面处理优先在盲孔子部件时制作完成,大大降低了表面处理的工艺难度。
3、超厚板二钻技术:将分步下钻改为预钻小孔+一次下钻11.5mm通孔、确保孔位精度控制。
4、超厚板成型技术:采用内定位+正、反控深铣,保证外形公差在±0.10mm以内。
(作者:石学兵 唐宏华 樊廷慧 陈春)
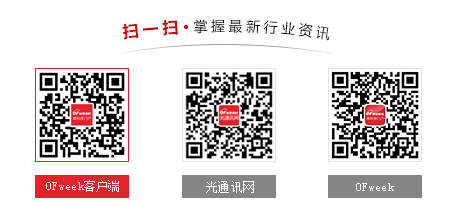
图片新闻
最新活动更多
-
7月30-31日报名参会>>> 全数会2025中国激光产业高质量发展峰会
-
7.30-8.1马上报名>>> 【展会】全数会 2025先进激光及工业光电展
-
免费参会立即报名>> 7月30日- 8月1日 2025全数会工业芯片与传感仪表展
-
精彩回顾立即查看>> 维度光电·引领光束质量分析应用全新浪潮【免费下载白皮书】
-
精彩回顾立即查看>> 2024(第五届)全球数字经济产业大会暨展览会
-
精彩回顾立即查看>> 【线下会议】全数会2024电子元器件展览会
推荐专题
发表评论
请输入评论内容...
请输入评论/评论长度6~500个字
暂无评论
暂无评论